目前,微电子技术得到了快速发展,机载电子产品呈现了小型化、轻量化的发展趋势,随之出现了热功耗、热流密度不断增大的问题。研究表明,55% 的电子设备失效是由温度过高引起的。与风冷技术相比较,液冷技术在高热流密度,特别是狭小 密 闭 空 间 的 工 况 下,散热优势更加明显。大功率电子器件的散热方式已从空冷向液冷转变。国外,机载液冷系统研究较早,如在俄罗斯的战斗机 Su - 27、预警机 A - 50,美国的预警机 E - 3C 等机载电子设备上采用了液冷散热技术。到第四代机,美国 F - 22 的电子设备热载荷已经高达 55 kW,其解决方案是采用综合热管理系统( ECS /TMS) 对全机热量进行管理和调控,该系统包含了液冷部分。我国在某先进战机上已经实现了综合热管理,高热流电子设备采用了环控液冷回路技术进行散热。航空电子设备的发展趋势为综合模块化,热功率更大,面临着百瓦级的模块的散热难题,而液冷技术是解决这一难题的首要选择。
本文总结了国内外相关标准规范,研究了设备组成,讨论了设计计算方法,旨在为综合模块化航空电子设备液冷散热设计与制造提供参考,为进一步研究方向提供建议。
目前,我国军用电子设备热设计领域重要的标准规范是由国防科学技术委员会发布的《GJB/ Z27—1992 电子设备可靠性热设计手册》,该标准中详细提供了液冷换热计算方法、冷却方式、冷却设计应考虑的问题、冷却系统的设计与计算、导热模块设计、热测试方法等,是我国军用电子设备热设计依据的重要准则。国外发展较早,也更加成熟,美国在 1978 年发布了《MIL - HDBK -251,Reliability /Design Thermal Applications》( 可靠性热设计手册) ,并被我国引入借鉴,该标准中提供了电子设备液冷的热设计方法。
综合模块化航空电子设备( Integrated Modu-lar Avionics,IMA) 的标准规范,国外研究较早,美国在 1994 年发布的 ARINC650,该规范中给出了外 场 可 更 换 模 块 ( Line Replaceable Modular,LRM) 的定义,促进了航空电子设备向综合模块化发展,其主要运用在民用航电设备。欧洲的联合标准航电设备委员会( Allide Standards AvionicsCouncil,ASAAC) 于 1977 年启动了 ASAAC PhaseII Contact 97 /86. 028 的标准研究工作,并于 2005年发布了降低费用、提高性能、改进操作的 LRM标准,该标准是目前综合模块化航空电子设备的最重要的技术标准,对军、民用航电系统有着重要影响,F - 22、F - 35 等参考采用有关技术和概念,我国在综合模块化航空电子设备的研究上也参考了该标准。
综合模块化航空电子设备的结构上主要由机架和模块组成,常见机架主要由单层和双层两种,由于双层机架结构较紧凑,承载模块数量较多,是研究的热点,如图 1 所示为一种典型的双层机架,其主要由面( 侧) 板、冷板、接头组成。
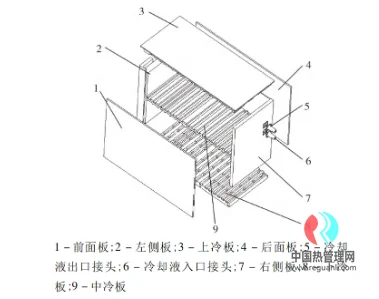
模块有两种结构形式,根据热功耗不同可设计成传导液冷和穿通液冷,主要区别在于模块内部是否进液,传导液冷模块最大允许功耗可达160 W,而穿通液冷模块可达 200 W 以上,如图 2所示。
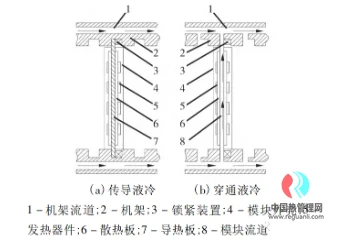
图 3 机架流道
模块的热功耗不断增加,为了提高其换热性能,通常是提高流速使流体处于湍流状态,或者优化流道走向,增加流体的扰动,但是这将明显增加流阻,增大了对载机冷却系统资源的需求,冷却资源有限,不能无限增加,微通道( 当量直径为 10 ~1 000 μm) 技术是解决在有限冷却资源的情况下大幅提高换热性能的有效方法。微通道液冷技术利用了传热微尺度效应和边界层强化换热机理,提高对流换热能力,研究表明,微通道技术能够满足热源极限热流密度 100 W/cm2的散热需求。大功率模块设计时,可考虑使用微通道技术。如图 4( c) 所示,为一种微通道的结构示意图。
液冷机架和模块多采用焊接成型。为兼顾重量和强度要求,机架和模块多采用铝合金,但铝合金导热率高,热量容易扩散,焊接时需要较高的集中热量; 膨胀系数高,易产生变形和缺陷; 液态时易溶解氢,产出“氢脆”现象。研究发现,搅拌摩擦焊、真空钎焊和真空扩散焊等焊接方式在铝合金的焊接中效果较好。
机架上的流道相对较大,可采用铝合金铣削成含有流道的腔体,然后与盖板进行真空钎焊或者搅拌摩擦焊,如图 5 所示。各个冷板焊接完成后可采用真空钎焊的方法焊接成机架,使机架内预先设计的各个流道相互连通,形成液冷回路。焊接时,要设计工装夹 具,并制定防变形措施。
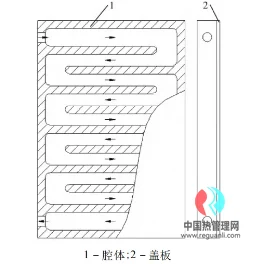
穿通液冷模块流道间隙小,钎焊时钎料容易堵塞且焊缝薄弱处容易渗漏,一般采用真空扩散焊,即在使用低于母材熔点的温度和不引起母材较大变形的压力下,通过表层原子相互扩散实现材料的连接,焊后组织、性能与母材接近。如图 6 所示,为一种翅片与盖板的扩散焊。
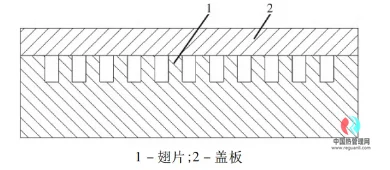
制定液冷方案时,冷却液的选择是首要问题,要综合考虑冷却液的冷却效果、流道特性、导电性和腐蚀性等各方面因素。机载设备的常用液冷剂主要由 65 号冷却液( 乙二醇水溶液,冰点为 - 65℃ ) 和 PAO( Poly - Alpha - Olefin,聚阿尔法烯烃)冷却液两种,国内主要应用 65 号冷却液,国外某超音速巡航飞机采用了稳定性较好的 PAO 冷却液。
对比两种冷却液,PAO 冷却液不导电、物性( 密度、比热容) 稳定; 但在体积流量或者质量流量相同的情况下,65 号冷却液比 PAO 冷却液有更加优异的冷却效果和流动特性。因此,65 号冷却液应用场景更广泛,但物性、绝缘性要求较高时,应考虑使用 PAO 冷却液。
冷却液本身对铝合金的腐蚀作用不强,但是在循环流动时,能够带动累积的微切削下的固体颗粒运动,加速冲蚀腐蚀。异物容易堵塞流体接头,导致流体泄露。要在循环系统中增加过滤,并定期清洗流道和更换冷却液。

冷却系统设计时,单机( 机载电子设备) 流阻与载机液冷系统的流阻分配值的匹配性关注度不高。单机流阻的大小能够影响载机液冷系统的工作负载。单机流阻偏大时: 单机本身获得的流量减少,降低了散热效果; 增加了载机液冷系统工作负载,增大了耗能。单机流阻偏小时: 单机流量会增加,加强了散热性能; 但会使得载机液冷系统不能在理论设计点工作,其它单机设备因获得的流量减少而降低其散热性能。故流阻的匹配性设计是否合理能够影响载机液冷系统及单机设备性能的优劣。
单机流阻考核要求一般是在指定冷却剂、温度和流量等的情况下,单机总压降符合一定的范围值。压降包括单机内部流道的压降和接插件( 用于连接载机液冷管路和单机流道) 的压降。单机内部流道压降主要包括沿程压力损失和局部压力损失: 沿程压力损失是由于流体相互运动产生的阻力及流体与流道摩擦引起的; 局部压力损失是由于流体的速度和方向发生变化引起的。接插件引起的压降由厂家提供。单机内部流道的压降计算如式( 3) 所示。


局部压力损失计算如式( 5) 所示。
式( 5) 中:
Δpc—局部压力损失,Pa;
理论计算较复杂,且冷板流道结构复杂,并不是均温板,故可先将流道简化成可计算模型,使用理论公式计算后,留出裕度,再利用计算流体力学( Computational Fluid Dynamics,CFD) 的方法进行计算。计算后提取流体温度、速度及压力云图等,在温度较大、流道盲区和压降较大等不合理区域调整流道长度、数量、走向、截面形状、串并联关系等后进行计算,多次迭代寻优以满足散热、压降等要求。
综合模块化航空电子设备热流密度越来越大,液冷散热是研究趋势,我国在该领域已经做了大量尝试,但是在如下方面尚需进一步开展深入研究: